A Roadmap for Electronic Product Design and Development
The electronics manufacturing process is challenging and sometimes very demanding. Due to unforeseen difficulties and product complexity, most hardware startups fail before their first innovative product hits the market. Thankfully, newer technologies, design techniques, and procedures have decreased the risk of failure in electronic device development, resulting in more successful products.
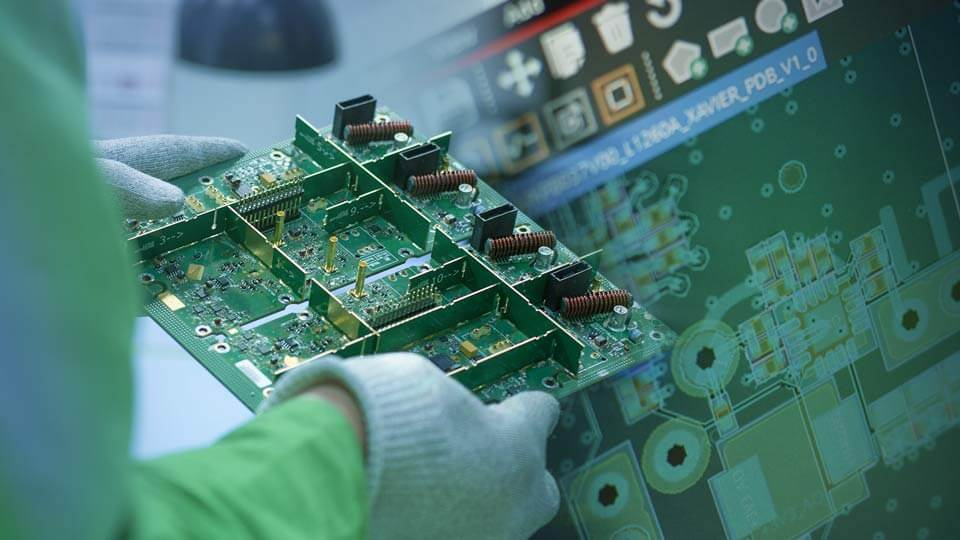
The process of electronic product designing, creating, and producing electronic hardware is known as electronic product development. Designing an electronic device starts with establishing the requirements, followed by creating a design proposal and project plan that details the expenses, timeline, and different segments of the design and manufacturing process.
In this article, we
will explore the essential phases of the electronic product design and development process
and how they come into play in the manufacturing of modern electronic products.
- Process of Electronic Product Design and Development
- Concept Development
- Creation of a Preliminary Production Design
- Estimation of Production Cost
- Creation of the Schematic Circuit Diagram
- Printed Circuit Board (PCB) Design
- PCB Prototyping
- Testing and Verification
- Design Refinement
- Documentation and Certification
Process of Electronic Product Design and Development
The process of electronic product development involves a sequence of steps that will guide you when transitioning from the ideation stage to the mass production stage. These stages are important and will help bring your project to life. They include:
Concept Development
The concept development stage is crucial to the success of any electronic product design process. It helps ensure that the product meets the needs of its intended audience, stands out in the market, and is technically feasible. Without a clear understanding of the product concept, the electronic product development process can be directionless and lead to a product that fails to meet expectations.
Going further into the market and identifying potential clients’ wants is also critical. If people are experiencing an issue that has yet to be solved, you may fill a market gap by providing a feature that addresses that specific demand.
Market research will allow you to assign a reasonable budget, define the business goals and technical feasibility, and establish optimal product parameters. You can gather the necessary information through focus groups, interviews with potential consumers, online surveys, and brainstorming sessions.
Thereafter, moving on to the next phase of turning the product idea into a profitable solution becomes easier—selecting the appropriate materials, technologies, and manufacturing processes to achieve the desired outcome.
Creation of a Preliminary Production Design
Several iterative methods are used throughout the preliminary production design stage to improve the product idea and design to ensure it satisfies the necessary criteria for functionality, durability, and quality. While creating the basic electronic production design, construct a system block diagram, which specifies each electronic function and its connectivity.
A microcontroller or microprocessor is needed for the majority of electronics, and numerous components—including displays, sensors, memory, etc.—interface with the microcontroller via various connectivity options. Making a system block diagram makes determining the kind and quantity of serial ports and other types of connections needed simple. This is a crucial initial step in choosing a suitable microcontroller for your product.
After creating a system-level block design, you can identify and choose suitable production components depending on your final product’s intended features and target unit cost. This will allow you to produce the preliminary Bill of Material.
Estimation of Production Cost
This involves calculating the expenses associated with the manufacturing and production process. By estimating the development cost early in the design process, designers and engineers can ensure that the product is designed within budget and can be produced profitably.
A bill of materials (BOM) is a detailed inventory of the raw materials, parts, and components required to create a unit of the product and the quantities of each.
Creating the Bill of Materials, determining the component costs, calculating the labour costs, and summing any additional charges, such as shipping fees, are all steps in arriving at a complete production estimate.
Following the BOM’s completion, each component’s cost is determined through market research or by asking for quotations from suppliers. Then, you can move on to estimate the labour costs by determining the time needed to manufacture the individual components and final product assembly.
This stage is essential as it helps ensure the product is designed within budget, and the designers and engineers can avoid unexpected costs during manufacturing.
Creation of the Schematic Circuit Diagram
In this stage, you will pay close attention to the small details like resistors and chips, and follow standard wiring and component placement rules. This will help ensure that the circuit is clear and free from errors.
To avoid mistakes, it is recommended to use an Electronic Computer-aided design (ECAD) or Electronic Design Automation (EDA) tool to create the schematic diagram.
Printed Circuit Board (PCB) Design
After finishing the schematic, you will design the printed circuit board (PCB). The physical board that houses and connects all the electrical components is known as the PCB. Often, the tools used to create the schematic diagram are also used to create the PCB layout. This type of tool’s notable features include the ability to route tracks, define the widths of the tracks based on the current flow, define component pad locations, and more.
PCB Prototyping
Electronic prototype development involves two steps. The bare, printed circuit boards are created in the initial stage. Using one file for each PCB layer; your circuit design program will let you output the PCB in the Gerber file format.
These Gerber files can be delivered to a prototype shop for lower volume runs. The identical files might be sent to a bigger manufacturer for higher production volumes.
The second step is soldering every electronic component to the circuit board. You may generate a file from your design program that displays the precise coordinates of each component on the board.
Testing and Verification
Once the prototypes are complete, the product will undergo a series of tests to ensure it meets the required quality, reliability, and functionality standards. This includes environmental testing, stress testing, and functionality testing.
Cost and time projections for this stage might be challenging. Naturally, any issues you encounter are unanticipated, so determining their cause and the best way to resolve them takes time.
The programming of the microcontroller is often done concurrently with evaluation and testing. To ensure the board has no serious problems, you need to perform at least some simple testing before you start programming.
Design Refinement
The engineering team may refine the product’s design based on the results of the testing and verification stage. This may involve adjusting the design of the components, systems, or products to address any issues identified during testing.
Documentation and Certification
Finally, the electrical engineering team will create detailed documentation that outlines the product’s design, functionality, and manufacturing processes. The production team will use this documentation to manufacture the product at scale.
Several forms of certification are required for all marketed electrical devices. Different certifications are necessary depending on which country the product will be marketed in.
Every Step is Critical—Choose VECTOR BLUE HUB today!
Electrical product development is a nonlinear process that can be frustrating due to the necessity to perform various iterations. Yet, commitment to the process is required.
At VECTOR BLUE HUB, our expertise and years of experience can guarantee a more seamless and straightforward process. From the concept stage to final product manufacturing, we are committed to delivering excellent service and support tailored to your needs.
Access the ideal combination of procedures and capabilities to enter the market swiftly and confidently.