Electronic Product Redesign: Critical Factors to Keep in Mind
Electronic products have revolutionised how we live, work, and interact with the world around us, playing an increasingly vital role in nearly every aspect of modern society. As technology continues to rapidly evolve, however, it’s becoming increasingly clear that many of these products will need to be redesigned to stay relevant and competitive.
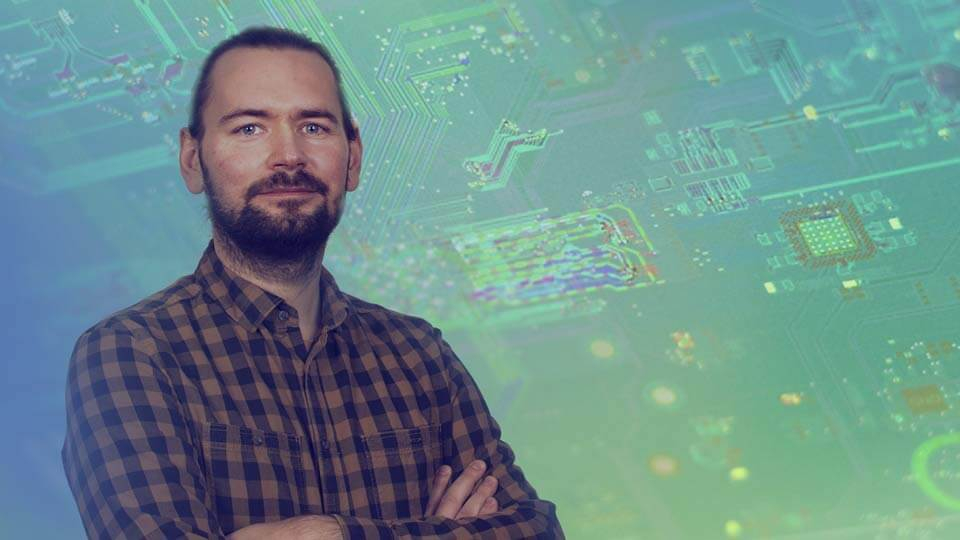
From improving functionality and aesthetics to reducing production costs and complying with changing regulations and component shortages, product redesign can offer a wide range of benefits for both consumers and manufacturers.
Gain insights into the latest trends and techniques in electronic product redesign from our CTO, Daniel Żywalewski and discover how your company can benefit from these innovations!
Table of Contents
- Redesign process—the rationale behind the change explained
- Chip shortages in the manufacturing process and product development
- 6 Powerful Redesign Tips
- 1. Replacing the hard-to-find components with more readily available ones that have similar specifications
- 2. Seek alternative suppliers who may have the parts you need in stock
- 3. Simplify the design of your product to use fewer components, which may help reduce the number of parts you need to source
- 4. Consider modular design and follow Design for Assembly rules
- 5. Increase your inventory levels of critical components to reduce the risk of running out of stock
- 6. Keep the certification requirements in mind from the beginning of the process
- Are You Ready to Improve Your Product Redesign?
Redesign process—the rationale behind the change explained
As industries continue to evolve and grow, it becomes imperative for businesses to frequently evaluate their electronic product design and development and make the necessary changes to keep pace with the changing landscape. The rationale behind the redesign process can vary depending on the objectives, resources, and desired outcomes, and understanding these reasons is critical to ensuring a successful redesign process.
Technological advancements
The fast pace of technological advancements often means that newer and better components become available, making it necessary for electronic redesign to take advantage of the latest technology.
Obsolescence
Older electronic products will become obsolete over time and redesign may be necessary to keep up with changing consumer demands and preferences.
Reducing manufacturing costs
Redesigning electronic products can also help reduce production costs using more efficient manufacturing processes and materials.
Safety and compliance
Safety standards and regulations may change over time, and redesign may be necessary to ensure that electronic products comply with these standards and regulations.
Improved functionality
Redesign can also help improve the functionality of electronic products by making them more user-friendly, easier to operate, and more reliable.
Aesthetics
The visual appeal of electronic products is vital to consumers, and redesign may be necessary to update the appearance of a product and keep it in line with current trends and styles.
Availability of components
This involves making changes to the design of a product to reduce its reliance on components that are in short supply or to substitute them with alternative materials that are more readily available.
Chip shortages in the manufacturing process and product development
The shortage of electronic components has been a problem for many years, but it has become more acute recently. Semiconductor manufacturers are facing the task of satisfying current demands in 2023 and fulfilling backorders caused by problems of the past few years.
Although they have invested more and expanded their capacity, achieving both mentioned goals simultaneously seems like a formidable hurdle. This has mainly impacted electronic product companies, which are experiencing shortages of critical components such as capacitors, resistors, transistors, and diodes.
Due to a surge in electronic product demand, production delays, and supply chain disruptions, it’s hard to predict whether the current electronics shortage will stabilise in the near future. These factors have created an unprecedented situation where many companies are struggling to source the necessary components to keep their businesses running.
As they cannot wring water from a stone, not surprisingly, they are turning their attention to seeking new ways of dealing with this situation when no replacements for materials are available. In favour of keeping the business profitable, more and more companies are deciding to change the design of the products they can no longer manufacture according to the current invention.
But how can you do that effectively? Click now to read the blog and elevate your product design to the next level.
Elevate Your Electronic Product Design: 6 Powerful Redesign Tips
1. Replacing the hard-to-find components with more readily available ones that have similar specifications
An experienced EMS partner is an invaluable resource in helping to replace hard-to-find components, having access to a vast network of suppliers and distributors that can help them source the required parts quickly and efficiently.
In addition, EMS partners have a design team of experts who are well-versed in component substitution, which means they can help identify and recommend suitable alternatives that can be used in place of the hard-to-find components.
2. Seek alternative suppliers who may have the parts you need in stock
EMS partners have a vast ecosystem of alternative suppliers who may have in stock the electronic components required to change the product design. They can leverage this ecosystem to find the right supplier with the necessary stocked parts. With their established relationships, EMS partners can also negotiate better prices and faster customer delivery times.
3. Simplify the design of your product to use fewer components, which may help reduce the number of parts you need to source
When designing a product, adding as many features as possible can be tempting to make it stand out in the market. However, a more complex product design often comes with a higher production cost, increased complexity, and a higher likelihood of failure. That’s why it’s essential to simplify your product design to use fewer components.
One way to simplify your product design is to start with a clear design brief. By identifying the problem your product solves and the essential features it needs to include, you can eliminate unnecessary components and reduce the overall complexity of the product.
4. Consider modular design and follow Design for Assembly rules
Another approach is to use modular design. Breaking your product into smaller, more manageable modules that can be easily connected will help you identify redundant components and reduce the overall number of parts. The flexibility you gain will help you implement changes and improvements during the following stages of the product lifecycle.
Choosing multi-functional components is another way to simplify your product design. Rather than having separate parts for each function, search for components that can perform multiple functions.
Following the mindset of Design for Assembly, it’s advisable to avoid complex shapes, multiple parts, and difficult-to-assemble components. Simplify the design as much as possible, to ensure the manufacturing process is more manageable and cost-effective.
5. Increase your inventory levels of critical components to reduce the risk of running out of stock
By maintaining higher levels of inventory, businesses can better manage supply chain disruptions, unexpected surges in demand, and delays in receiving new material lists. However, this should be addressed with the cooperation of a knowledgeable EMS partner who has a broad ecosystem of partners and will help you with stocking your inventory.
6. Keep the certification requirements in mind from the beginning of the process
Understanding the regulatory environment and compliance standards is critical in ensuring the new design passes certification. The redesign process must take into account the required standards, and any changes should ensure that the product meets the requirements, as failure can result in legal penalties and reputational damage.
Recertification can be a lengthy and costly process, which can impact the time-to-market of the redesigned product. Companies should consult with regulatory authorities early in the design process to avoid costly delays to ensure the new design meets the required standards. This consultation can identify potential certification issues early in the design process, allowing for adjustments to be made before the product is manufactured.
In some cases, recertification may not be necessary for a product redesign. Minor changes to a product that won’t affect its safety or performance may not require recertification, and some standards may allow for a streamlined certification process for certain types of product modifications. However, the requirements for such changes should be carefully considered to avoid any potential regulatory or legal issues.
Are You Ready to Improve Your Product Redesign?
At VECTOR BLUE HUB, we pride ourselves on delivering innovative solutions that fulfill customer requirements. Our experienced engineers use the latest software and tools to create schematic diagrams, printed circuit board (PCB) layouts, footprints, and other design documents.
One of the key advantages of working with VECTOR BLUE HUB is our commitment to quality. We use only the highest quality materials and components in our designs, and we rigorously test every part to ensure that it meets our standards for performance and reliability.
Whether you need a complete electronic design or crisp consultation on electronic redesign, our engineering team have the expertise and experience to help you succeed.