IoT Product Certification: Case Study
Certification of an Internet of Things (IoT) electronic product is one of the main challenges for tech companies today. IoT products are quickly becoming a part of modern life, and their popularity is encouraging governments to step in and increase their safety regulations.
Not surprisingly, many customers seeking to introduce a product to the marketplace desperately need help to complete the certification process, as they are overwhelmed by the rules and certification requirements. This case study of an IoT product certification process examines the testing stages and why having a lab environment is second to none for a manufacturer.
IoT Devices – The Long Story Short
IoT has huge potential in the way it transforms the way businesses operate in various industries. The ubiquitous networking of physical objects through IoT has enabled a multitude of exciting applications that affect our everyday life. New technologies, ecosystem players, IT professionals and finally industries are all working together to provide exciting new services and capabilities.
In order for everything to work well together, there needs to be a strong foundation for the communication technology upon which everything is built. One of the most important aspects which is lacking is deployment. Without the correct tools and frameworks, these connected devices can become misconfigured, leading to problems that could have been avoided had they been appropriately tested. So here is the challenge that enterprises need to define:
Where do they want to deploy their new products, as this decision will determine the scope of the required tests for certification. The more complex and risk-encumbered the area is, the better the company must be at knowing how to navigate between the terms and discussing the requirements.
The date when the product is to be introduced to the mass market.
How do they want to process it all – by outsourcing to the industry’s leading experts or by conducting the whole process themselves.
As part of our comprehensive electronic product certification services, we have been helping many companies to understand and implement their IoT product development strategy. We have also been responsible for providing them with IoT product certifications to ensure that their products comply with the relevant industry and connectivity standards, as well as the government regulations regarding security, environment, and privacy.
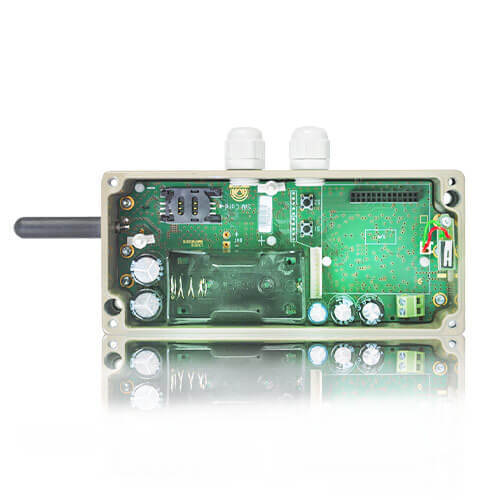
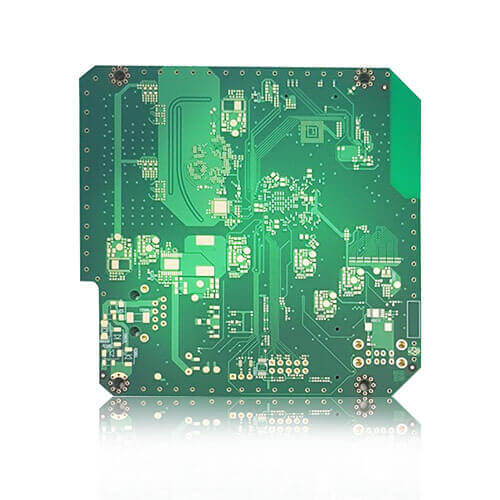
One of the most challenging but eventually successful projects from the last few months concerned the certification of IoT devices for the US market. How did we manage the project risks and navigate through the functionalities and configuration of the IoT product, keeping high performance as a top priority? Let's dive in!
IoT Device Certification Case Study Explained: Improved sensitivity for LTE in band 12 (700MHz)
Over the years, VECTOR BLUE HUB and one of our customers who specializes in the industrial IoT sector have built a strong partnership, bridging the need for innovation to accelerate the delivery of key IoT technologies in the public space. Due to our relationship based on transparent communication, flexibility, as well as quick and effective decision-making, we were asked to conduct the certification process for another IoT device to be deployed in the US market.
The product utilizes the frequency range from 699 MHz to 716 MHz , also known as LTE band 12, which is commonly used for public services and emergency frequencies.
It had to pass PTCRB certification – organized by the Cellular operators of North America to test all mobile phones, M2M devices, IoT devices, and other similar hardware operating on mobile networks.
Scope of the performance tests:
Radiated Spurious Emissions
UCIC electrical SIM tests
OTA antenna performance – Total Radiated Power (TRP) and Total Isotropic Sensitivity (TIS)
IoT Project Stages
Stage 1 – Scrutinising Product Security and Functionality
We're always looking for new ways to improve. It's important to us that our customers have the best possible experience, whether they're testing their IoT devices or getting them certified.
When we started working with customers, they had a prototype of their IoT device. As part of our process, we perform verification tests to make sure that all requirements are included in the prototype. We found out that there were some minor issues with the prototype, so we introduced corrective actions to make sure that it met all requirements.
Because we were so invested in delivering a high-quality product, we introduced corrective actions immediately to make sure that everything was ready for certification.
In the end, securing customer satisfaction and gaining assurance that our prototype was well-prepared for the IoT device certification was more important than anything else—including time pressure and budgetary concerns.
Stage 2 – The Three Musketeers in Electronic Manufacturing Services: Engineering Validation Testing, Design Validation Testing and Production Validation Testing
Engineering Validation and Testing – this stage was crucial in checking if all functional requirements match the specification. Once the hardware tests provided the results and metrics expected in the specification, the product was ready to enter another stage – Design Validation Testing.
Here, we verify whether components, chassis, and other elements form a coherent whole as a tangible product or if there is space for improvement; it is the last call to fix the design. Once all this happened, engineers prepared the unit for regulatory certifications and environmental protections.
Next, moving to Production Validation Testing – the results from the test has a decisive influence on the quality and cost of series production. Only minor changes are allowed in the PVT phase. Any significant change to the design triggers a return to the DVT phase.
The outcome of the three above-mentioned stages was positive, meaning the prototype contained the desired functions and met all certification requirements.
Stage 3: TIS Failure: What was the cause?
What tests the device underwent are determined by its design and the technologies used. As a device that was based on wireless technology, it had to go through Total Radiated Power (TRP) and Total Isotropic Sensitivity (TIS) tests. Thanks to the fact that we have built a wide ecosystem of partner and supplier networks over the years, we benefited from performing the tests in a specially adapted laboratory.
While the results of the TRP measurements were satisfactory, the results of the TIS test fell short of the required standard. Together with the team, we carried out a wide range of internal tests to find out the cause of the problem. What does such a process look like? Below is the result of one of the first brainstorms of our engineering team:
Stage 4: Investigation and Conclusions
In search of the disturbance source, we built a special chamber in our laboratory to improve the sensitivity of the device so that it could pass the final certification. Due to COVID, this was the only rational solution, which ultimately accelerated the preparation of the product for certification.
Conclusions
The disturbances depend on the power voltage – the highest with 9V DC
Disturbances depend on the current consumption
Disturbances are the highest when the probe is close to the DC/DC converter in the CELLULAR MODULE
Source of disturbances ▶ DC/DC converter
Stage 5: Modifications
Using our advanced lab and its state-of-the-art equipment, we were able to gain leverage in debugging and finding the leading cause of issues. We implemented the necessary modifications, and as a result, we managed to protect the electronic PCB from the DC/DC disturbance converter.
The job has yet to finish, although the parameters worked as intended. Ahead of us was the chore that usually gives many engineers goosebumps and sleepless nights – preparing the certification documentation. But not for engineers from the VECTOR BLUE BUB team. We quickly managed to transfer the necessary materials so that our customer could launch the product before the date fixed.
Let VECTOR BLUE HUB lead your next success story!
VECTOR BLUE HUB has proven knowledge in certification programs, bridging the innovation and security gap between technology and business. Depending on the type of certificate required for introduction into the market, our technical support can help you with:
- CE, UL and FCC certification process support
- EMC, LVD, RED, and ROHS directives
- US/Canada and worldwide certification support
- Test & Validation