Quality management in electronic devices industry
Project in electronic devices industry, if successful, comes from what the client wants and what the market expects. Between them springs up quality – the bridge between a company and its clients. Quality planning is then answering the question how to deliver what is in demand. But why does it take so much to plan this very process, especially in manufacturing electronic devices, and when to call quality enough?
Quality in manufacturing electronic devices
entails many departments and people to be planned. Especially when it is
outsourced. As one of the fastest growing trends in the electronics industry, it
looks day by day more attractive to many businesses which now more often contract
their production outside to cut the costs down or reduce time to launch the
product on the market. From the first scratch to the assembled device a lot
might change – compatible technology, demand or politics. No matter the change,
all comes down to not overpaying for the production. This is why you should
plan the quality of a product.
And there are many issues that can make the
plan veer unexpectedly:
Undue output – producing too much, or even not enough, is a
real threat in case of the changing market demands.
Lack of information – fast tempo, multi-tasking or information
clog leads to missing what is going on in the project.
Unbalanced workload – keeping quality on a desired level needs
properly distributed people among their work stations to maintain the work
flowing the right pace.
Incompatible manufacturing speed – magazine stock, assembly stations
and tests – they all need smooth and easy progress.
Non-compliant product – such an outcome is the result of
an unorganized quality control management and that, speaking of control, is a real control light
for the whole process.
Not too cold not too hot –
quality management
Non-compliant product is realistically the
worst scenario that can happen to any outsourcer. Too broad and general
guidelines will more than sure mislead the team to create a product of unwanted
features. Saying: “It must be good,” says, in truth, nothing.
Giving too general guidelines and trying for
the product to be the best of the bests is a risky business. Adopting an unclear or short product design
specification can result in the launch of an unwanted product on the market,
and, of course, the loss of a lot of money. On the other hand, exhaustive specification
guidelines may clog somewhere in the gorge of the company’s operational
tactics. After many days spent on mastering only one feature, it all may come
up as unnecessary, while it only needed to be better supervised by a quality control manager, who sees the process as a whole and knows where to switch the
track.
“A proper plan opens the gate to potential
marketing the product. In VECTOR BLUE HUB we work closely with clients at every
stage of the project to understand their needs and finally give them the
optimal solution,”
says Piotr Krauze, Quality & Reliability Assurance Director.
The market is changing and it is essential to optimize
the product by ongoing working on its vitality.
“We simply answer the question if anyone still
needs this particular product with these particular specifications?” Piotr
points out.
Investing in quality reduces
time
Having both design and manufacturing divisions
on board entails quality management as mandatory. The later the stage of
quality control is introduced to the project, the more costs weigh down the end
product, and that results in not delivering the end value. Too little attention
paid to quality increases the risk of later service costs, complaints or even
loss in the future business opportunities. Too much scrutiny, however,
decreases maintenance costs but increases the entry level, namely, the price.
The whole game swings around the point in the middle – to deliver satisfactory
product quality together with low costs of investment and maintenance.
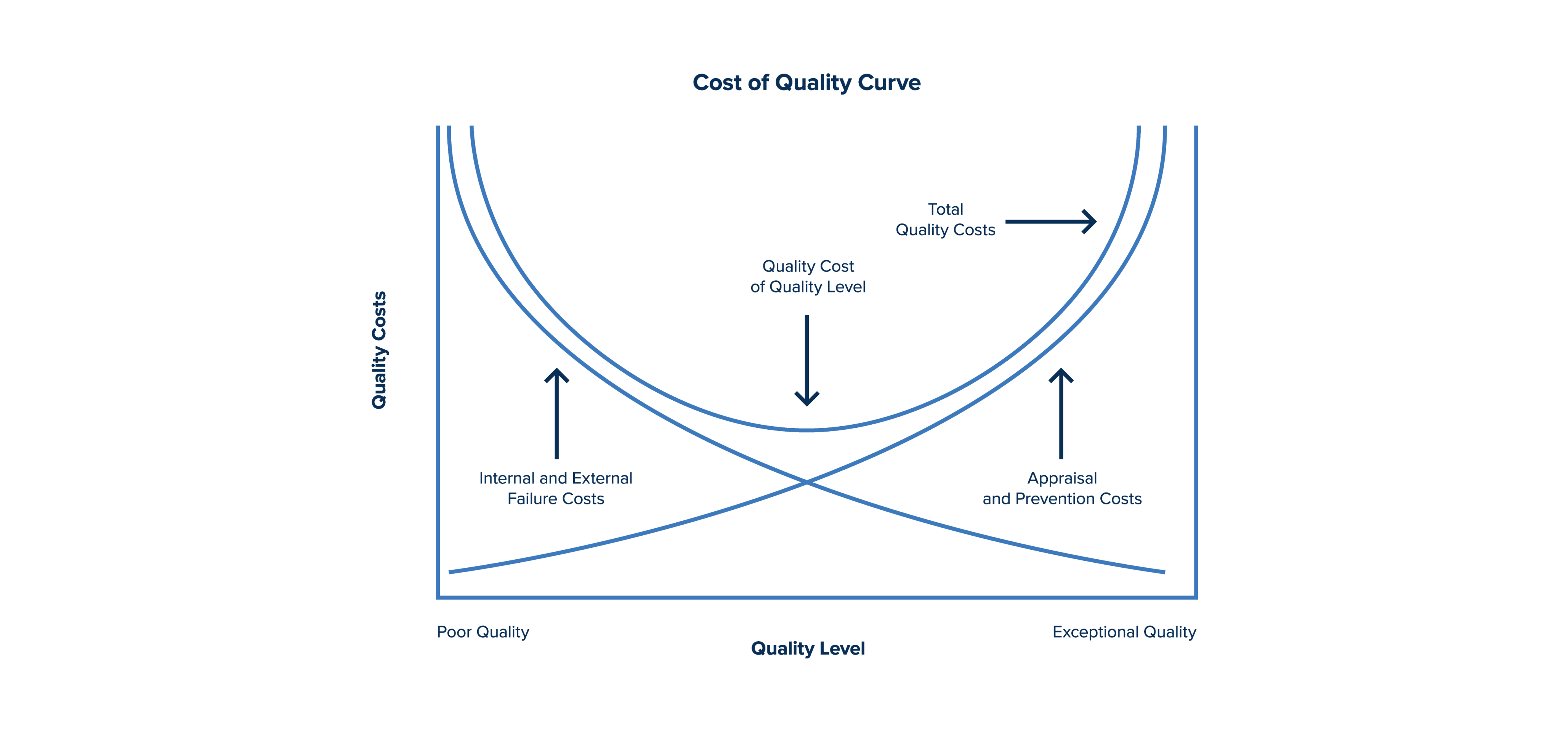
Keeping quality on track
Quality assurance in development and
manufacturing electronic devices is not a static, once settled decision. To
keep it going the right track there come invaluable tools which, when planned
and rightly implemented, make the quality process smooth. The range of such
tools reflects best what quality management really is – it is a touchpoint of a
company and the market. Quality sees the company from the helicopter view and
it goes across the divisions and departments to assure that all the resources
contribute to sustaining what the clients expect.
Tools of quality management:
Process. That reflects the broadest scope of all
tools. It incorporates continuous improvement, ongoing optimization and adjusting
the product to the market. A well-planned process answer to the problems
concerning risk management. Components short supplies, market niche satiation
or shorts in the workload – they all needed to be named as the risky points.
After the process is planned, there comes the moment for the next tool.
People. They are not only engineers responsible for
technical improvement and development, but also managers who keep eye on
whether tasks stay open or fall into the done category.
Traceability system. It track components, manufacturing
itself, gather data in real time and does everything to reduce human error. It
is constituted by the laboratory, thorough documentation and IT softwares for
work organization.
Certification. These documents are the best proof that
a company has acquired some requirements which will guarantee repeatability of
product quality. A certificate says that someone from outside the company has
accredited the way the job is done.
Quality management in huge part is about
overall managing the project. That is why it takes so much so many people into
organizing it. Planning, let us say it, prevents unpredicted spendings, even if
at the beginning it calls for some. The answer when to say enough to quality
development is at the moment when the market need is covered with a
well-managed product. The wanted and bought outcome is the best proof for the
best quality. Quality is nothing more, thus, than a language between the end
user and the producer, as it allows them to fulfill their needs.