SMT Assembly: Advantages and Applications
Surface Mount Technology (SMT) is a vital process that is transforming the electronics industry. In this article, we delve into the intricacies of SMT assembly, exploring its advantages over through-hole technology, the applications in which it is used, and the process involved in its implementation.
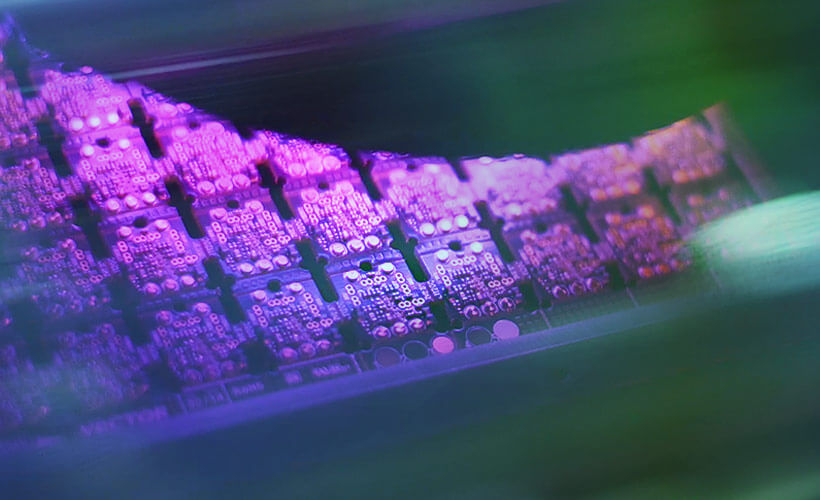
Through a detailed description of SMT components, equipment, and materials, you will gain valuable insights into this innovative technology which can streamline production and improve overall performance.
What is SMT Assembly Technology?
Imagine a world where electronic devices are smaller, lighter, and more efficient than they are today. A world where complex circuits are seamlessly integrated onto tiny printed circuit boards reduces the need for bulky components and makes manufacturing processes more efficient. This is the world of Surface Mount Technology (SMT) Assembly, a revolutionary manufacturing process that has transformed the electronics industry.
With SMT Assembly, electronic components are mounted directly onto the surface of a PCB, eliminating the need for through-hole parts. This creates smaller and more complex circuits, resulting in smaller and more efficient devices. In addition, the SMT Assembly process is faster and more cost-effective than traditional through-hole assembly, making it an attractive option for manufacturers looking to streamline their production processes.
What is SMT assembly process?
Surface Mount Technology (SMT) is a modern method of soldering components directly onto the board's substrate in their designated locations – soldering pads. SMT Assembly is commonly used for applications that require solid mechanical bonds on the finished PCB. Unlike the traditional method of inserting wires through holes in the board, surface mount technology employs solder paste to affix components to the board's surface. This technique allows for smaller electronic components, which can significantly reduce the PCB's size.
SMT is also a quicker assembly process than a conventional assembly – Through-Hole Technology THT – and can be optimised using Pick and Place PCB assembly machines to precisely prepare all the components. SMT components are also generally less expensive than THT components, making SMT a more cost-effective option for PCB assembly if cost and space are critical factors.
Stages of the SMT Process
The Surface Mount Technology (SMT) process has revolutionised the electronic manufacturing industry, enabling the compact and efficient assembly of electronic components on printed circuit boards (PCBs). SMT has become the cornerstone of modern series electronics production by integrating advanced techniques, such as solder paste printing, automated component placement, and precise soldering.
What are the most crucial stages that drive the SMT process forward, shaping the modern electronic landscape? See below!
1. Solder Paste Printing
The solder paste printing stage is a crucial step in the surface mount technology process for electronic component assembly on a printed circuit board (PCB). Delicate and precise, it demands the experience and expertise of skilled engineers to apply solder paste with meticulous accuracy onto the PCB.
The success of this stage lies in the intricate interplay between component size, pad dimensions, and specifications outlined in the datasheet. It is fascinating to witness how the quality of the entire SMT line hangs in the balance, with any imperfections during soldier paste printing potentially impacting up to 60% of the overall defects.
2. Placement of the components with the use of Pick & Place machines
Utilising sophisticated robotic systems, this stage ensures accurate positioning of components with exceptional speed and efficiency. The pick and place stage in the Surface Mount Technology process involves the precise placement of electronic components on a printed circuit board (PCB), considering each component's unique parameters.
Different passive elements, such as capacitors and resistors, are applied with high speeds, while components requiring greater precision, such as IC, BGA, FPGA are handled at lower rates. The average operating speed of the Pick and Place machines is approximately 50,000 components per hour, ensuring efficient and accurate assembly of electronic devices. This stage showcases the flexibility and adaptability of SMT processes, catering to diverse component requirements while maintaining high productivity levels.
3. Reflow soldering
Reflow soldering is integral to the Surface Mount Technology (SMT) process, where an appropriate thermal profile must be tailored individually to each board. During this process, selecting the correct thermal profile is crucial to accommodate various factors, such as the type of board, the components mounted on it, and number of layers.
A well-prepared thermal profile takes into consideration the specific temperature process window within which the components and laminates can be safely soldered over a given time. Achieving the ideal balance between larger and smaller components is essential. Smaller parts require only a slight temperature increase during soldering to ensure proper bonding, while larger ones demand a higher heat input to ensure adequate solder joint formation. Therefore, meticulous profiling tailored to the individual requirements of each element is of utmost importance in reflow soldering, providing successful and reliable connections throughout the assembly process.
4. Automated Optical Inspection – AOI 3D
The Automated Optical Inspection (AOI) stage has emerged as a fundamental part of the Surface Mount Technology (SMT) process, replacing traditional methods, such as visual inspection and manual examination using microscopes or magnifying glasses. Manufacturers have been compelled to automate their operations with the continuous miniaturisation of components. As a result, every element on the circuit board undergoes meticulous verification efficiently.
The AOI 3D system examines the presence of each component, ensuring its correct labelling and proper polarity. It also meticulously inspects all solder joints to ensure they meet the required standards. This automated inspection stage has significantly enhanced the efficiency and accuracy of quality control in SMT assembly, allowing for more reliable and precise electronic manufacturing with high repeatability.
Surface Mount Technology Advantages
SMT technology's popularity has grown as electronic devices become smaller and more complex. It is an excellent choice for manufacturers looking to produce compact, efficient, and cost-effective devices. The SMT Assembly process is widely used in various industries, from consumer electronics to telecommunication and industrial IoT.
By utilising SMT technology, manufacturers can reduce the device's overall size while maintaining or improving its performance.
Here are some of the primary benefits of SMT:
Smaller Components and Boards: SMT components are much smaller than through-hole components, allowing more parts to be packed onto a smaller board.
Higher Component Density: The ability to pack more components onto a smaller board also leads to higher component density, resulting in higher performance and more advanced functionality.
Improved Electrical Performance: shorter signal paths, reduced lead inductance, and higher frequency capabilities, all of which will enhance the electrical performance of the device.
Faster and More Efficient Electronic Assembly: The SMT assembly process is faster and more efficient than through-hole assembly, which involves automated assembly using Pick And Place machines. This results in a lower cost of production and increased production speed.
Possibility of full automation of the SMT process from PCB printing through assembly to AOI 3D inspection
Great opportunities to optimize production costs through automation and repeatability of the SMT process while maintaining high quality levels.
Surface Mount Technology – the cornerstone of VECTOR BLUE HUB manufacturing’s capabilities
SMT assembly technology is a fundamental process in electronic manufacturing, and at VECTOR BLUE HUB, we have intentionally selected equipment that is tailored to our specific type of electronic production. We have optimised our twin Juki SMT lines to provide maximum flexibility in manufacturing.
Our manufacturing plant is equipped with:
2 state-of-the-art SMT lines: Line Scan Technology in solder paste printing and Line Scan Technology inspection ensures comprehensive inspection coverage, as well as highly precise measurements of paste deposit height, area, and volume.
Our SMT lines are equipped with IFS-NX – Intelligent Feeder Management System. IFS NX controls the components on the feeders and mounted on the PCB in real-time. It improves performance by reducing the set-up time while ensuring the highest quality.
Multi-zone reflow soldering, enabling individual adjustment of the thermal profile to the components used on the PCB. With full zone control, precise soldering is possible with optimal process window settings.
Full 3D inline AOI system: Our complete 3D inline AOI system has been specifically developed for larger board sizes, providing accurate measurements for comprehensive inspection of components and solder joints on PCBs measuring up to a maximum of 510 x 460mm (20.1″ x 18.1″). The system is capable of inspecting even the smallest chip size.
Nitrogen ERSA wave soldering system: In our manufacturing processes, we utilise a coated solder module that delivers exceptional solder quality and consistent results thanks to the use of various wave formers tailored to specific applications. Additionally, nitrogen control is implemented through a rest-oxygen monitor to maintain the desired oxygen (O2) level in the nitrogen atmosphere.
A separate Setup Area with the NX infrastructure system supervising the warehouse, the correctness of the feeder settings, and adjustment to the requirements of the tapes, trays, and tubes. It also contains dry cabinets to protect components sensitive to moisture t from damage and adverse environmental conditions.
Experience flawless SMT assembly for your electronic devices by reaching out to our team of skilled professionals. Contact us today to guarantee a seamless manufacturing process.